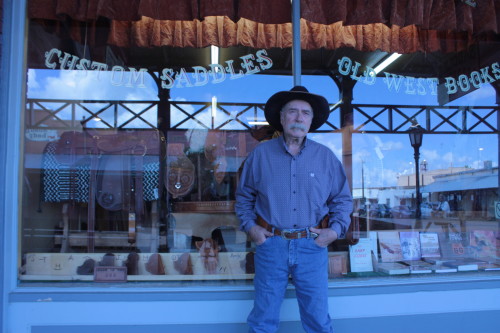
Walk into Tombstone Old West Books and sense years of cowboy history.
Stroll toward the back. Past the many rust-colored saddles with detailed designs of flowers, stars and other intricate patterns. Listen as the wooden floor creaks when passing by the shelves that showcase holsters and chaps.
Here one finds Geno D’Ambrose, surrounded by various cuts and colors of leather, at his workbench. Here is a craftsman, a saddlemaker, a vanishing breed in the country.
The warm, comforting aroma of leather lingers throughout the store. Behind the counter is D’Ambrose’s workstation, cluttered with taxidermy deer heads, rifles and pictures of him from mounted shooting events.
D’Ambrose huddles over a small desk illuminated by a blue desk lamp and covered in cuts of leather. He holds a flap of rawhide steady with his hands as he carefully carves etchings of vines into it with a hammer and awl.
To D’Ambrose, the art of saddlemaking is a rewarding craft and despite the fact that it is a fading tradition, he still looks forward to coming into work on a daily basis. He is a quiet, reserved man approaching the end of his middle-aged years who likes to let his leather crafts tell his life story for him.
He has made custom saddles for big names in the rodeo culture such as actor Ben Johnson and five-time world champion team roper Jake Barns. Depending on the size, purpose and the intricacy of designs on the saddles, D’Ambrose’s saddles can range from anywhere between $3,000 to $6,500.
His interest toward saddlemaking first sparked when he was living in Payson 30 years ago. There, he used to help a saddlemaker at his store while guiding and outfitting in the area.
D’Ambrose’s desire to learn the art of making saddles was limited, due to the store’s small size and lack of sufficient workspace. He wanted to branch out and learn more about the art so he decided to contact a saddlemaker in Springerville who was offering lessons.
“He taught me the basics and I kept at it,” D’Ambrose says. “I worked with him for about three months during the summer, came back to Payson, opened up a little store, started doing repairs, doing a little bit of tooling and making a couple of saddles. Been doing ever since and I love it.”
After his days in Payson he moved to Cave Creek in 1998. However, D’Ambrose and his wife took a dislike to the busy environment so he relocated his store to Tombstone in 2003 and named it Tombstone Old West Books. “I used to come down here for mounted shooting and I just like the town,” D’Ambrose says. “I like the small town, cowboys, just the atmosphere.”
Prior to his relocation D’Ambrose would be scheduled to make one or two saddles every month. Today D’Ambrose’s store is less busy and he sells saddles and other leather products primarily to tourists who visit. His website also offers a variety of leather products including saddles, holsters, belts and chaps.
If saddlemakers take their time and pay attention to intricacies in design, a plain saddle can take a minimum of 80 hours to craft. “When you start getting fancy with a lot of tooling it takes a lot longer,” D’Ambrose says.
A saddle consists of many different components, some of the important ones being the tree, fenders, rigging dees, and stirrup leather. The tree is the body or the base on which a saddle is made.
Fenders are the leather flaps on the side of the saddle that prevent friction between the horse’s body and the rider’s leg. Rigging dee’s are the D-shaped rings on the side of the saddle that attach to straps that hold the saddle secure to the horse’s back. The stirrup leather connects the stirrup, the part where rider’s feet go to gain leverage, to the saddle.
The tree is the main component of a saddle and it determines size of a saddle as well as the length of the seat. D’Ambrose orders his trees from a tree maker at Timberline Saddle Trees in Utah.
The method of covering wood trees with rawhide started at the beginning of the 1800s. D’Ambrose strays away from using fiberglass or Ralide trees as he frequently saw screws break into the rigging dee when he used to do repairs.
“I still do the old way to do it,” D’Ambrose says. “Old way is the best way.”
Quality leather is also a crucial component to a saddle. D’Ambrose uses leather from Herman Oak of St. Louis, Missouri, and Wickett and Craig in Pennsylvania. Both are American leather tanneries which he prefers over South American tanneries.
When putting together the other parts such as the fenders and stirrup leather, the saddlemaker must make sure that the saddle fits both the rider and the horse. “If it don’t fit that horse you’re not gonna go too far without putting sores on its back,” D’Ambrose says.
D’Ambrose has been riding horses all his life. He has two at his home that he and his wife ride. They use his handcrafted saddles.
He prefers making older style saddles to conventional saddles used for roping, team penning and reining. “1870’s-1900 turn of the century saddles, what they call half seat slick forks,” D’Ambrose says. “I do a lot of those. I like building those.”
It took D’Ambrose 10 years to master the art of saddlemaking. When learning, he found tooling to be one of the hardest parts.
D’Ambrose says one of the most memorable saddles he’s ever made was the one he made for Jake Barns as a donation for a charity. D’Ambrose decorated the saddle with ample silver he had custom made by a Navajo Indian silversmith.
Despite there being few saddlemakers left in the country, D’Ambrose is keeping the art alive at Tombstone Old West Books.
“I still after 30 years can’t wait til I get in here to build something,” says D’Ambrose. “Whether it’s a holster, or saddle, or pair of chaps, or a hand tooled belt. Whatever it is.”
Yuji Miyaji is a reporter for Arizona Sonora News, a service from the School of Journalism with the University of Arizona. Contact him at [email protected]
Click here for a Word version of this story and high resolution photos.